Stainless Steel 310/309
STAINLESS STEEL 310
- GENERAL PROPERTIES: The Chromium-Nickel alloy has a density of 0.290 lb/in3. Its modulus of elasticity of 29.0 x 106 psi. The specific heat capacity of Grade 310 is 0.12 Btu/lb ˚F.
Under intermittent service, Grade 310 shows excellent resistance to oxidation up to 1035°. In continuous service, it shows resistance to oxidation up to 1050°C.
It is also resistant to sulfidation and carburisation. The electrical resistivity is 30.7 microohm-in. It is non-magnetic, both in the non-annealed and annealed conditions. The chances of loss of Oo ductility are very less, and the alloy remains durable and sturdy. - CHEMICAL COMPOSITION: The type 310 consists of 24-26% Chromium, 19-22% Nickel, 2.00% Manganese, 1.50% Silicon, 0.045% Phosphorus, 0.030% Sulfur and 0.25% Carbon. The high chromium enables reduced sulfur atmospheres containing Hydrogen Sulphide. The combined effect of Chromium and Nickel enable high resistance to oxidation.
- CORROSION RESISTANCE: The Chromium and nickel content give Grade 310 high resistance to corrosion. However, the resistance is not applicable for corrosive liquid service. At temperatures, 550 – 800°C, the alloy will be, sensitised to intergranular corrosion caused by the segregation of impurities at the boundaries.
Liquids containing chlorides at extreme temperatures more than 100°C can be corrosive for the alloy. Thus, it can cause corrosion cracking. The alloy does not consist of the constituent molybdenum. It leads to a lack of pitting resistance. - WELDING: The welding of type 310 can be done, with matching electrodes like AWS A5.4 E310-XX and A 5.22 E310T-X and filler metal like AWS A5.9 ER310. There is no heat required before and after the welding process.
However, there is a possibility of the formation of high-temperature oxides on the surface after welding. For this, pickling and dormant passivation of the surface can be done. After welding, annealing should be done to restore any loss of corrosive resistance.
FABRICATION AND HEAT TREATMENT: The standard methods can readily form the alloys.
HOT WORKING: The hot forging for grade 310 is carried out in the temperature range 975 – 1175°C.
COLD WORKING: Grade 310 can go through cold working by stamping, drawing, upsetting etc.
ANNEALING: The Annealing is done by heating to the temperature range 1040 -1065°C. The alloy is then held, at that temperature for some time. This step ensures that the toughness of the material is retained.
HARDENING: Heat treatment cannot ensure any hardening of the alloy. The hardness has to be increased only by cold working like Grade 309.
309 Round Bars
309 Hex Bars
309 Square Bars
309 Flat Bars
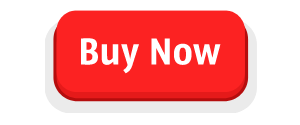
STAINLESS STEEL 309
- GENERAL PROPERTIES: This Iron-Chromium-Nickel alloy has a metric density of 8 g/cm3. It shows ductility and can be, readily formed. Under non-cyclic operations, it usually resists oxidation 1900°F (1038°C). This type has a melting point of 1455 °C. It has a tensile strength of 620 MPa, and it scores 85 on the Rockwell B scale. It indicates that it is very tough and durable.
The modulus of elasticity for Grade 309 is 200 Gpa. Specific heat capacity of this alloy is 0.12 BTU/lb-°F (32 – 212°F). It shows an electrical resistivity of 30.7 Microhm-in at 68°C and 78 Microhm-cm at 20°C. It can also be utilised, in slightly cementing, oxidising, thermal cycling and nitriding applications. - CHEMIAL PROPERTIES: It consists of 60% Iron, 23% Chromium, 14% Nickel, 2% Manganese, 1% Silicon, 0.2% Carbon, 0.045% Phosphorous and 0.03% Sulfur.
- CORROSION RESISTANCE: Under wet, corrosive environments, alloy 309 will not be able to function. The creep properties are, enhanced by the carbon content present in high amounts. It tends to cause harm to the corrosion resistance for aqueous environments. After Iron, chromium ranks second in the highest percentage within the alloy.
Chromium delivers a high corrosion resistant property to the alloy. If the alloy is exposed, to high temperatures for long durations, it will become a subject to intergranular corrosion. For sulfur content up to 2 g/m3, under continuous application of 1922°F oxidation can occur. For sulfur content greater than 2 g/m3, the maximum temperature for oxidation is 1742°F.
FABRICATION AND HEAT TREATMENT: The material can be readily formed and fabricated through heat treatment. The common and standard fusion or resistance methods used for other alloys can be used, for Grade 309. However, the Oxyacetylene welding method does not apply to this alloy.
HOT WORKING: This process enables the mechanical deformation of the alloy. It takes place at 1177°C (2150°F). The reheating is done, at 982°C (1800°F) after which it can be, quenched rapidly.
COLD WORKING: Grade 309 is reshaped in this process through heading, drawing, upsetting, stamping.
ANNEALING: For annealing Grade 309 stainless steel, the temperature has to be at 1038-1121°C (1900-2050°F) to reduce internal stress. It is followed by quenching in water. This step ensures that any lost corrosive resistance is, regained. Through this treatment, it is, assured that all the carbides are in solution.
HARDENING: Hardening of type 309 can only happen through cold working. The heat treatment doesn’t contribute to the hardness of this alloy.